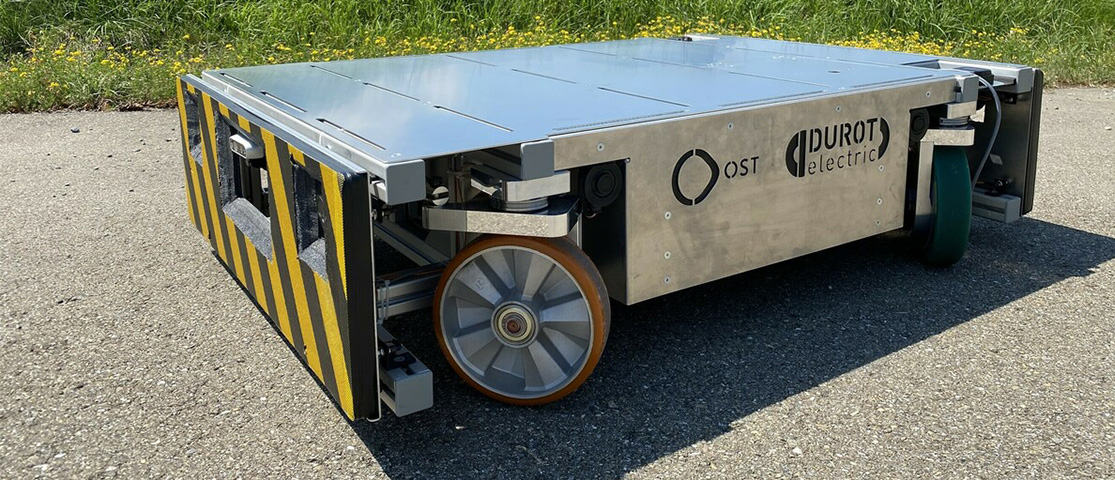

As a precise digital image, the digital twin makes it possible to analyze complex issues in electric commercial vehicle development at an early stage. The simulation of drives, energy storage and cooling systems opens up a wide range of possible applications, from concept studies to efficient decision-making aids for battery capacity and charging solutions.

Aim and purpose of a DigitalTwin
It is not uncommon for the development of a battery-electric commercial vehicle to take up a lot of resources. Drives, energy storage and cooling systems must be designed during the concept and design phase. The question then often arises as to which concepts work best and where optimizations can be made. In order to be able to consider such complex issues at a very early stage of development, Durot Electric has developed a DigitalTwin – an exact digital image of a battery electric commercial vehicle – together with the University of Applied Sciences OST in Eastern Switzerland and the Institute for the Development of Mechatronic Systems (EMS). MathWorks Simscape® serves as the simulation environment for the DigitalTwin.
The DigitalTwin can be used in many different ways. The generated model serves as a basis for future concept studies and developments. It can be adapted to other vehicle architectures and re-parameterized. This makes it a very valuable tool during development and model maintenance. Concepts and different components can be better assessed during development. During model maintenance, new components or special functions can be simulated before components have to be purchased or integrated. By simulating real operating cycles, electrical, mechanical and thermal relationships (complex systems) can be better interpreted and optimized. Last but not least, it can be used as a decision-making aid for the battery capacity to be specified or the need for a fast-charging solution (CCS). Supported by simulation results, there are significant cost and time savings.
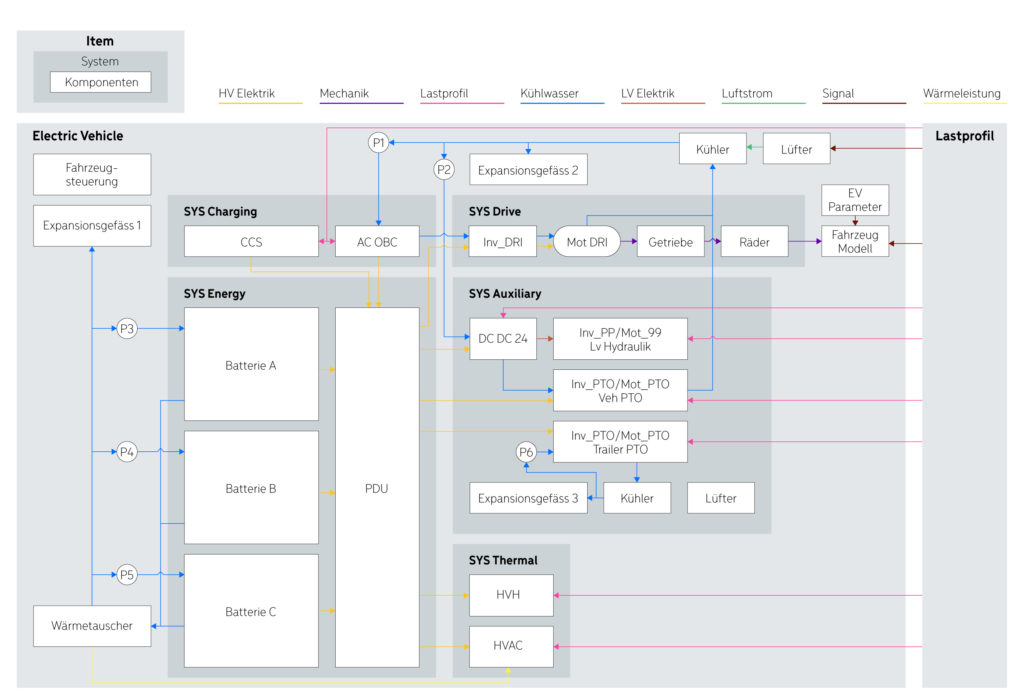
The challenge of implementation and validation
In the first step, the vehicle subsystems (battery, traction drive, auxiliary drive, charger, etc.) must be considered in isolation. Some parameters can be derived from the manufacturer’s specifications, but often assumptions and simplifications have to be made. In order to consolidate these assumptions and achieve a more accurate model, the components can be identified in a further step on the test bench or in the vehicle.
The subsystems are combined in the model according to the desired system architecture. Different variants are also possible, which can later be compared with each other during the simulation evaluation. Despite many assumptions and simplifications, a fairly precise system behavior can already be achieved in the first run.
When developing the basic model, we focused on simulating the battery storage system, the drivetrain and thermal management. However, we have also included the auxiliary drives and charging technology in a simplified model structure.
The biggest challenge is the thermal system analysis. Due to a lack of reliable data from the component documents, the thermal behavior of the individual subsystems can only be simulated to a certain extent. For more precise modeling, more precise data must be obtained in consultation with the supplier, or the component must be identified itself.
With the electrical and mechanical simulation results, on the other hand, precise system behavior is achieved much more quickly. In most cases, the manufacturer’s specifications are sufficient for complete parameterization.
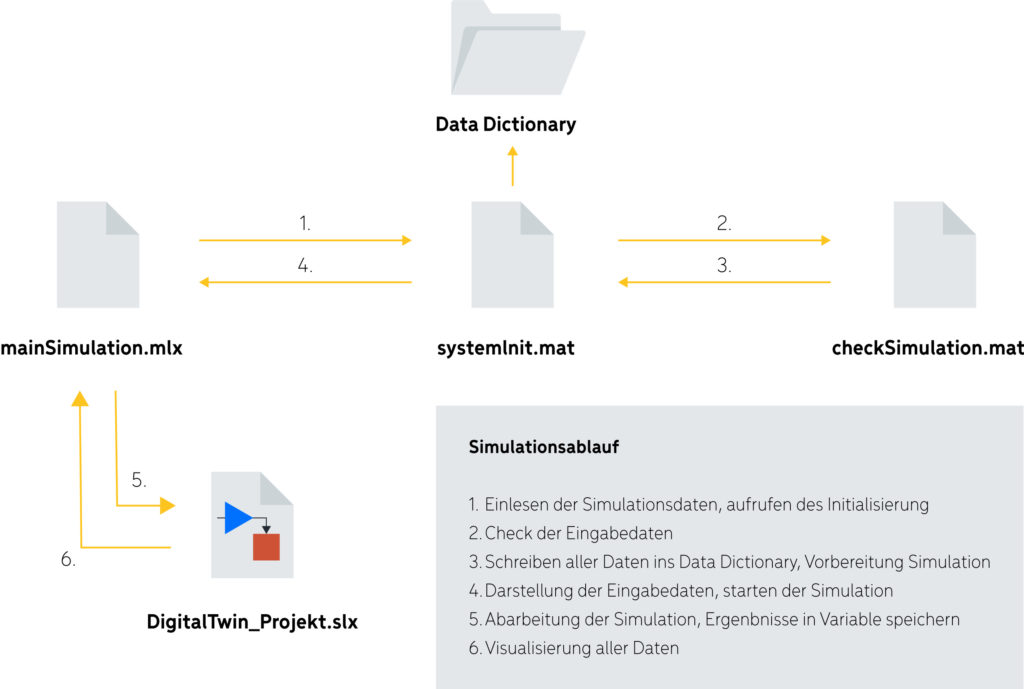
Operating the DigitalTwin and running a simulation
Using our basic model as an example, we were finally able to compare it with measurement data from the real vehicle. This led to the realization that the system characteristics of the individual components and systems were well mapped. The current state of the simulation shows a good approximation of the real vehicle with a simulation deviation of less than 10% and can be used for further simulations or developments in this area.
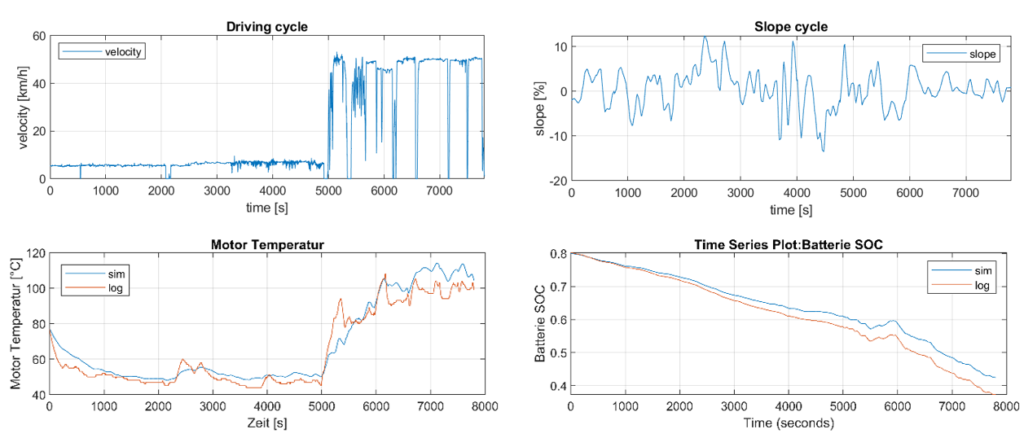
Simulation results of the DigitalTwin
Next steps
The DigitalTwin was deliberately designed to be very generic, with a model architecture that can be quickly adapted to other vehicle concepts. At the same time, MATLAB® scripts were developed to help us extract component parameters from the manufacturer’s specifications and convert them into a correct format for the simulation.
In the long term, we want to create a database with the most important components that we can reuse, optimize in the long term and increase accuracy.
With this basis, we will be able to develop even more precise and detailed concept studies for our customers in future and keep the initial outlay to a minimum.